Two & Three Wave Highway Guardrail Full Automatic Production Line
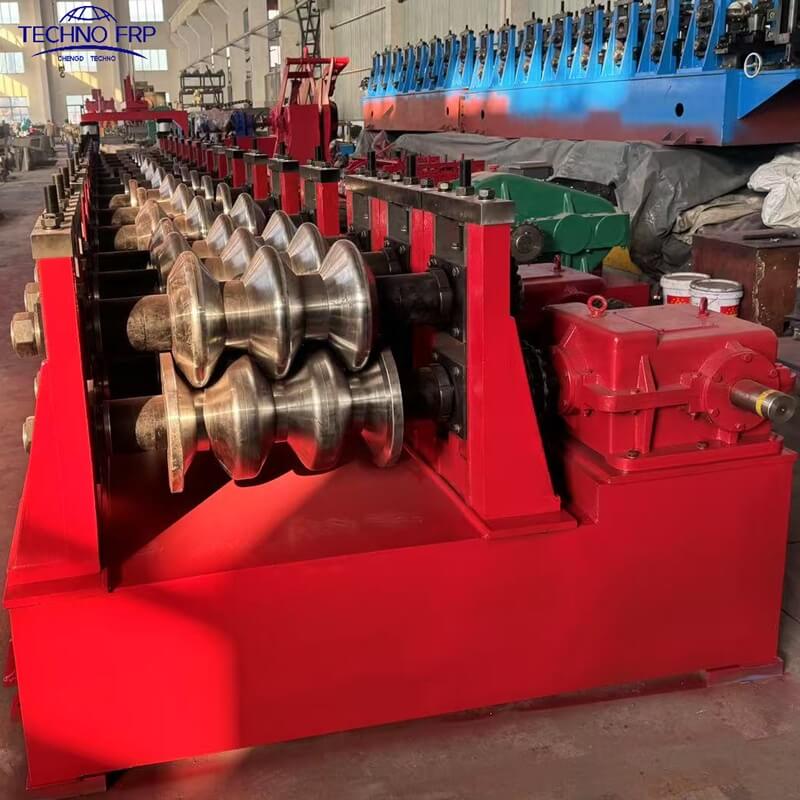
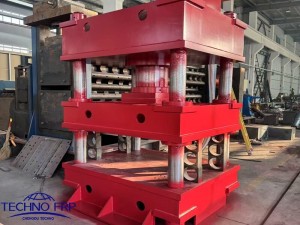
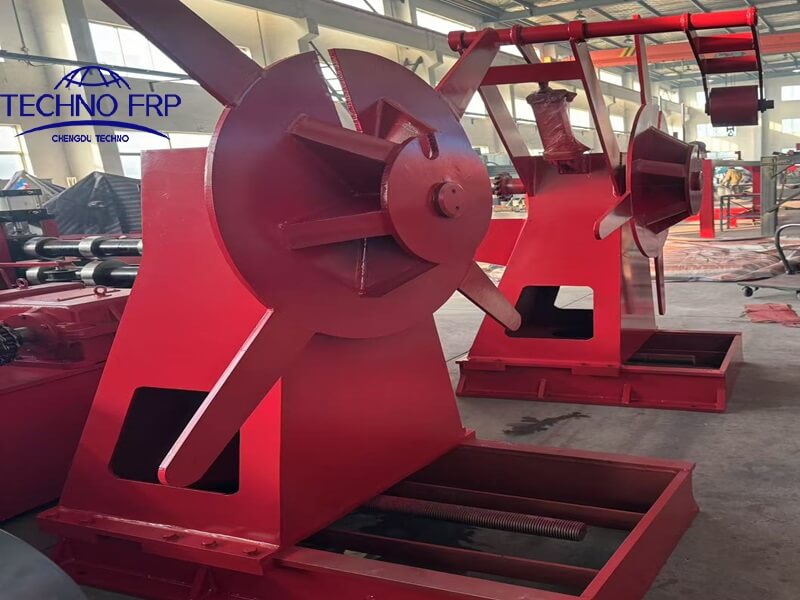
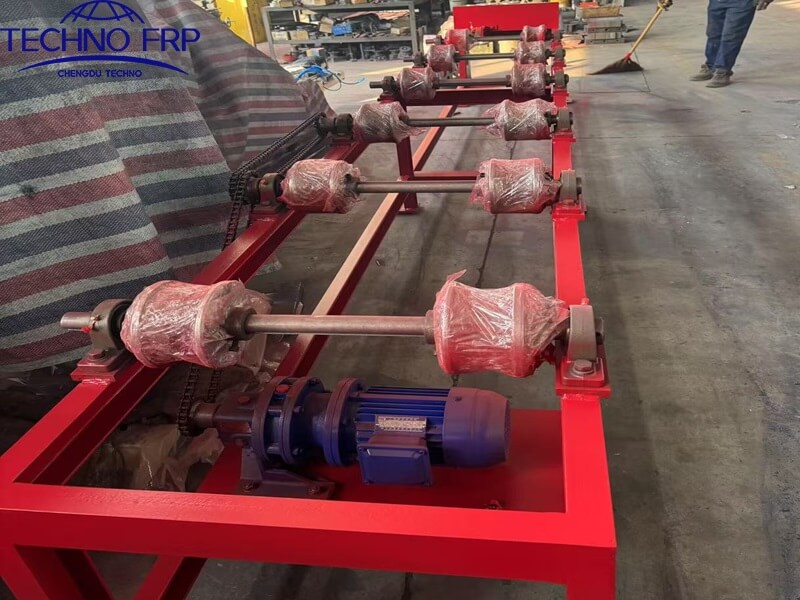
Full Automatic Steel Two or Three Wave W Beam Highway Guardrail Production Line
The two- or three-wave guardrail production line is a set of high-efficiency, high-precision, fully automatic cold-bending forming equipment developed to protect the safety of high-grade highways. It is specially used to produce double-corrugated guardrails (W-type guardrails) and three-corrugated reinforced guardrails commonly seen on highways. This type of guardrail has good impact resistance and flexibility and is widely used in road safety protection projects, playing a role in separation, collision prevention, and preventing vehicles from running out of the road.
The entire production line is automated, from unwinding, leveling, punching, cold-bending, and fixed-length shearing to the finished product collection of raw steel strips, with simple operation and high efficiency. Techno’s equipment adopts a modular design and can be flexibly configured according to customer needs to meet the production needs of different corrugated plates and hole types.
This highway guardrail production line is stable, convenient, and easy to maintain. It is an ideal equipment choice for transportation facility manufacturing companies, steel structure processing plants, and high-speed guardrail supporting manufacturers.
Highway W Beam Guardrail Forming Production Line Process Flow
Raw material preparation - uncoiling - leveling and feeding - encoder sizing - automatic punching - fast feeding - cold forming - fixed length cutting - material collection rack - finished product
Optional extended process:
• Automatic stacking system
• Online marking/printing
• Galvanizing/spraying (with back-end surface treatment equipment)
• Bending (for curved guardrails)
• Corrugated plate folding device (to enhance structural rigidity)
Whole Guardrail Line Production Flow Chart
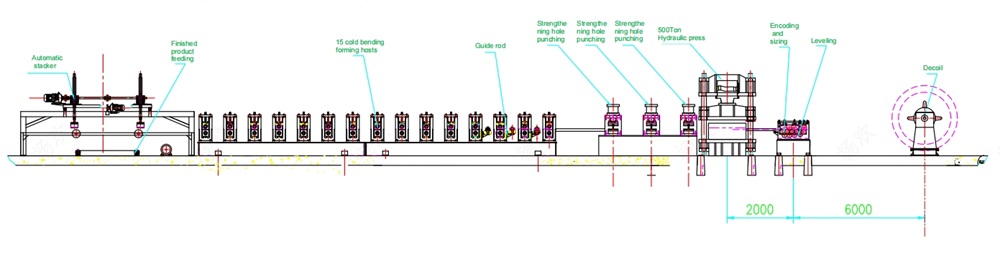
Main Equipment of 2 or 3-Wave Highway Guardrail Production Line
Double cone power discharge and uncoiling, with a load-bearing capacity of 15 tons and a speed increase of 508mm to 650mm in the inner diameter range of the steel coil. The 5.5KW cycloidal pin wheel reducer is used as the uncoiling power mechanism for automatic discharge, reducing the time and personnel required for material replacement. The power part can smoothly feed the steel strip into the guide and leveling unit.
The wall panel type 9-roller leveling machine has dual bearings at both ends of the flat roller. It can be controlled by forward and reverse movement in manual mode. The leveling roller’s diameter is 135mm, and its material is 40 Cr. The heat treatment is HRC48 º to 52 º. The leveling machine has guide vertical rollers at the front and rear, and a feeding port is equipped with a pressure device.
An imported pulse encoder measures the length, which can be modified on the electric cabinet’s touch screen according to actual production needs.
The cold roll forming machine is the core equipment of the high-speed guardrail production line, which is responsible for gradually pressing the punched steel strip into a standard corrugated guardrail (double or triple wave). The equipment is deformed successively through multiple forming rollers to ensure that the plate has high forming accuracy, consistent waveform, smooth surface, and no indentation, which is the key guarantee for the quality of the finished products of the entire production line.
Structural composition of roll forming machine
♠ Frame structure: High-strength welded frame structure, aging treatment to prevent deformation.
♠ Forming roller group: 13 to 18 rollers are designed according to the product model, made of GCr15 or Cr12MoV, quenched, hardness HRC58-62, to ensure high wear resistance and service life.
♠ Transmission system: Chain or gear transmission, the main motor is speed-regulated by the frequency converter, and the operation is stable.
♠ Pressure roller support seat: The left-right symmetrical structure is adopted to ensure uniform force and uniform deformation of the waveform.
♠ Adjustment mechanism: Manual screw or electric screw adjustable pressure device, convenient for adjusting steel strips of different thicknesses.
♠ Discharging guide rail: Ensure that the guardrail plate, after forming, is stably transitioned to the shearing section.
Technical parameters of roll forming machine
Project | Parameters |
Sheet width | 480~750mm |
Sheet thickness | 2.0~4.0mm |
Forming speed | 8~15m/min (adjustable) |
Forming passes | 13~18 lanes (designed according to corrugated plate) |
Main motor power | 15~30kW (customized according to output) |
Roller material | GCr15/Cr12MoV, heat treatment and quenching |
Forming accuracy | ±1.0mm((whole plate length error) |
Control system | Linked with the PLC system, automatic detection, and shutdown protection |
Roll-forming machine features
✅ High forming accuracy: symmetrical waveform, high dimensional consistency, meeting national standards such as JT/T281.
✅ Stable and durable structure: An industrial-grade steel structure frame is used, which will not deform during long-term operation.
✅ Long mold life: The high-frequency quenching roller is durable and wear-resistant, reduces the frequency of mold change, and saves maintenance costs.
✅ Strong compatibility: It can be switched with different types of guardrail molds and is suitable for double-wave/triple-wave and other multi-specification production.
✅ Convenient operation: modular design, easy maintenance, equipped with emergency stop button and overload protection device.
The servo fixed-length shearing machine is a key piece of equipment in the high-speed guardrail production line for accurately shearing the formed corrugated guardrail to the set length. The equipment uses a servo control system to achieve high-speed conveying and precise positioning of the plate. The shearing tool moves quickly, the cut is smooth and burr-free, and the consistency of the finished product length and quality stability are ensured. It is an important part of the whole line automation.
Features of servo cutting machine:
• High cutting accuracy, error ≤±1mm.
• High alloy shearing blades are used, and they have a long life.
• It can be linked with the PLC control system to achieve full-line synchronization.
The automatic stacker receives and neatly stacks the finished guardrail panels after cutting. It is convenient for packaging and handling. Its features include:
1. Automated operation: The palletizing process is completed fully automatically, reducing the need for manpower.
2. Efficient and accurate: Sensors and servo motors ensure accurate stacking and improve production efficiency.
3. Flexible stacking method: Supports different stacking modes to adapt to guardrail panels of different specifications.
4. Safe and stable: Equipped with safety protection devices to ensure safe operation.
5. Interfacing with production lines: Seamlessly connect with other equipment to ensure smooth operation of the production line.
6. Low maintenance cost: High durability design reduces failure rate and maintenance costs.
Techno's Advantages
• The PLC control system is automatically and easily handled.
• Easy operation: key in the length and quantity on the control panel.
• We use a gearbox-driven machine and a servo feeder system for punching to ensure that this production line can produce W-beam highway guardrails with high precision and strong power.
• Guarantee of quality: Techno guarantees that the highway guard rail roll forming line design is in accordance with the client’s required drawing. The machine is brand new. The specification and performance are as stipulated in the drawing, and the operation is smooth and good.
• The 2 or 3-wave highway guardrail automatic production line can be customized according to your special requirements.